Export ready American built machines in stock, shipping from Miami
Keeping the Money Flowing: Essential Vending Machine Maintenance Tips
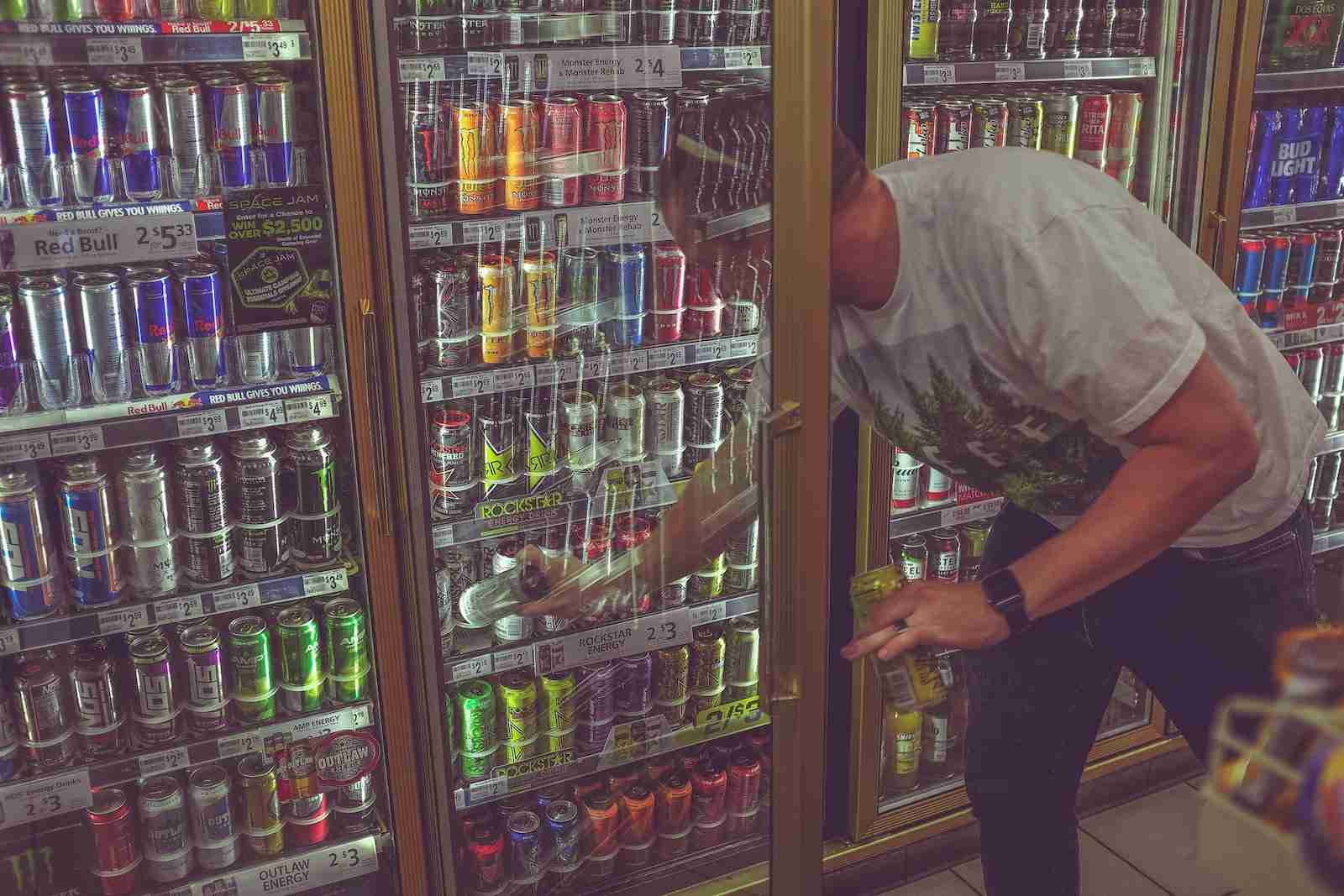
Vending Machine Maintenance Tips are the cornerstone of ensuring a smooth and profitable vending operation. In a world where convenience is king, the last thing any operator wants is a machine that’s out of order or not performing at its best. Proper maintenance doesn’t just ensure continuous revenue; it also extends the lifespan of your machine and solidifies your reputation as a reliable vendor. Let’s delve deeper into the essential tips that can keep your vending machine running efficiently.
Introduction to Vending Machine Maintenance
The pathway to efficient vending machine operations hinges on a fundamental aspect: maintenance. Just as a vehicle requires regular tune-ups to ensure optimal performance, a vending machine demands periodic checks and care. While the initial investment in a vending machine can be substantial, proper maintenance ensures that this investment yields consistent returns over time.
By understanding the nuances of vending machine maintenance, operators can prevent potential machine downtimes, which could otherwise lead to lost sales and a tarnished reputation. Moreover, a well-maintained machine exudes professionalism, instilling confidence in users about product quality and hygiene.
Embracing a proactive approach to maintenance, rather than a reactive one, is key. This involves scheduled checks, prompt troubleshooting, and understanding the common challenges that vending machines might face. By doing so, one not only ensures seamless operations but also extends the machine’s lifespan.
Basic Vending Machine Maintenance Tips
A pristine appearance is paramount. The aesthetic appeal of a vending machine directly impacts a user’s decision to approach and use it. Regular cleaning, both internally and externally, not only ensures efficient functionality but also reinforces customer trust. After all, a clean machine signifies attention to hygiene and quality.
Routine inspections serve as a machine’s first line of defense. By periodically checking critical components, operators can identify and rectify potential issues before they escalate. This can range from ensuring products are adequately stocked to checking the functionality of the coin and note acceptors.
Another vital aspect is addressing residue build-up, a common challenge especially in machines dispensing drinks or sticky snacks. Over time, spills or leaks can lead to sticky residues which might hamper functionality. Regularly cleaning spill trays, checking product alignment, and ensuring the machine is level can significantly reduce such occurrences.
Troubleshooting Common Vending Machine Issues
Despite the best efforts, occasional hiccups in vending machine operations are inevitable. One frequent issue operators encounter is a jammed coin mechanism. Such a problem, while common, can be swiftly addressed. Regularly clearing obstructions, cleaning pathways, and occasionally recalibrating mechanisms can alleviate such concerns.
Product dispensing issues, another challenge, often arise from improper product loading or misaligned components. Addressing these promptly is essential to ensure consistent sales and maintain user trust. Ensuring that products are loaded as per the manufacturer’s guidelines, aligning dispense pathways, and occasionally resetting mechanisms can rectify such issues.
Lastly, with the advent of digital vending machines, software glitches have become a concern. These can manifest in various forms, from display errors to payment hitches. Regular software updates, periodic system checks, and maintaining open communication with machine manufacturers can mitigate these challenges.
Preventive Measures to Avoid Downtime
Preventive maintenance is worth its weight in gold when it comes to vending machine operations. Ensuring that the machine is in top-notch condition, even before issues arise, can significantly reduce unplanned downtimes. First, maintaining a regular servicing schedule, in accordance with the manufacturer’s guidelines, helps in early problem detection.
Next, keeping an updated record of the machine’s maintenance history offers insights into recurring issues, if any. It also aids in tracking servicing schedules, warranty deadlines, and parts replacements. A well-documented maintenance log becomes invaluable for making informed decisions about replacements or repairs.
Lastly, training staff or operators in basic troubleshooting skills can be a game-changer. While they might not replace a technician’s expertise, they can address minor issues promptly, ensuring that the machine remains operational while awaiting expert intervention.
Establishing a Relationship with Vendors
A strong relationship with machine vendors and suppliers ensures that an operator isn’t left stranded during technical glitches. Such partnerships facilitate quicker response times during breakdowns, access to original replacement parts, and insights into the latest maintenance practices.
Vendors, being the machine’s creators or suppliers, possess a deep understanding of its workings. Regularly consulting them for maintenance advice, updating on any observed anomalies, or seeking guidance on optimization can significantly boost machine performance.
Furthermore, in an era of rapid technological evolution, staying in sync with vendors provides operators with updates about software patches, new features, and even training sessions. This not only extends the machine’s life but also enhances its functionality and user experience.
Ensuring Proper Power and Electrical Care
Power fluctuations, surges, or abrupt outages can wreak havoc on vending machines, especially those with digital interfaces. Ensuring that machines are connected to stable power sources, preferably with surge protectors, becomes pivotal to their longevity.
Routine checks on power cables, plugs, and outlets help detect wear and tear or potential hazards. Replacing frayed wires or damaged components not only ensures consistent machine operation but also averts potential safety risks.
Periodic consultation with an electrician, especially when installing new machines or shifting existing ones, guarantees that power requirements are met adequately. This aids in avoiding overloads or electrical mishaps, thereby bolstering machine safety and efficiency.
Safety Measures and Vandalism Prevention
Vandalism and theft are unfortunate realities that vending machine operators occasionally face. However, with strategic placement and security measures, these risks can be mitigated. Installing machines in well-lit, high-traffic areas can deter potential vandals, as the risk of being observed or caught increases.
Investing in security cameras or surveillance systems not only acts as a deterrent but also provides evidence in case of any untoward incidents. It’s equally vital to ensure that the machine’s lock systems are robust, occasionally updating or changing them to prevent unauthorized access.
Moreover, working closely with venue owners or managers where the machine is placed can foster a sense of shared responsibility. Their assistance in monitoring or reporting suspicious activities can significantly reduce vandalism incidents.
Conclusion: Investing in Long-Term Machine Health
Vending machine maintenance isn’t just about immediate fixes; it’s a long-term investment ensuring consistent profitability and extended machine lifespan. With vigilant care, routine checks, and a proactive approach, operators can minimize disruptions, maintain customer trust, and maximize their returns. After all, a smoothly running vending machine is the heartbeat of this unique entrepreneurial venture.